Restaurant Supply Chain Management
Originally Posted on FoodableTV – By Doug Radkey 04/03/2017
Depending on the size of your restaurant model and the size of your menu, the restaurant supply chain can be simple to some and complicated to others. With raw materials, food safety regulations, delivery logistics, best-before dates, and overall packaging to coincide with your often limited storage capacities, the system can become one that sticks together or untangles on you in the blink of an eye.
When it comes to restaurants, bars, cafes, and food trucks; the producers, manufacturers, delivery drivers, owners, managers, and servers ultimately share the responsibility to create a safe and enjoyable dining experience within your concept.
It is imperative that your food service business understands the supply chain of the product it serves, in addition to having an emergency plan in the case a link of the supply chain “breaks.” This is now more important than ever at the restaurant level, with the farm-to-table and garden-to-glass movement; plus the continuous growth of craft beers, local distilleries, and of course, wineries.
Transparency, traceability, and accountability must be a top concern when deciding on vendors to ensure all products (both food and beverage) entering your restaurant or other food service business, are not only safe for your customers, but for your community.
Consider what a food-borne illness or product recall will do to your image, productivity, margins, and overall bottom line. The challenge with an illness or recall is the unpredictability of when it will happen, but the solution is to be more proactive and understanding at the restaurant level.
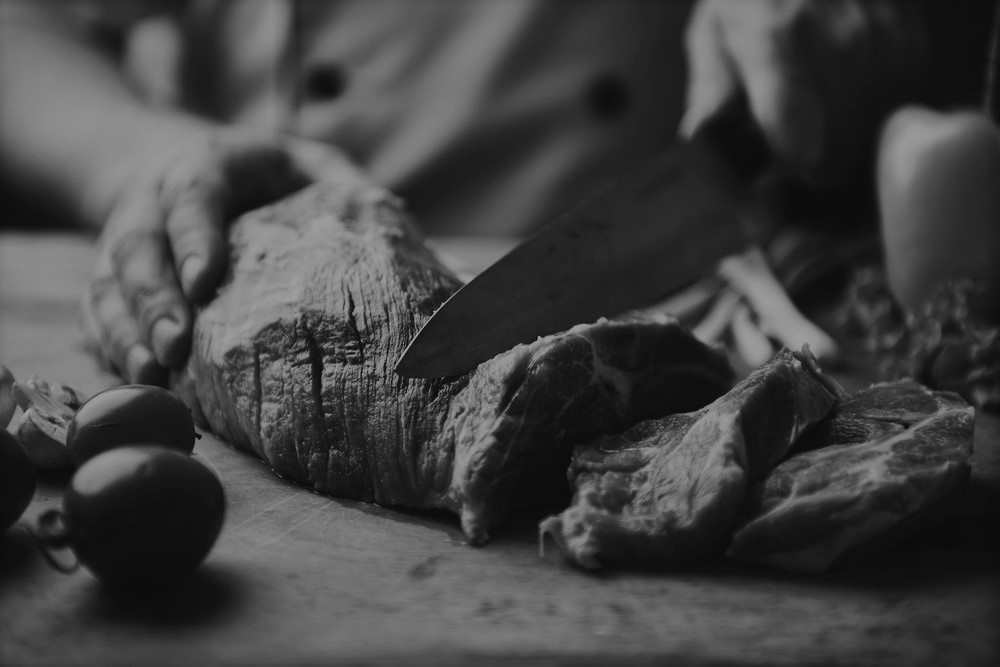
Initial Planning
At a more local level, this is more easily managed, whereas at a corporate or chain restaurant level, planning can become much more difficult. The most ideal situation is to deal directly with certified growers, co-ops, or distributors as much as possible who meet a high level of government standards. You need to reduce your risk by eliminating as many third parties as possible. When planning your menu(s), keep them compact and look for ways to re-purpose ingredients as much as possible. This will allow you to list out a limited number of targeted suppliers, including data on their company history, any past recalls, their storage facilities, delivery logistics, and ethical working environment.
Multiple Vendors
Freshness and seasonality play a large part in many restaurants across the nation. Outside of just delivering quality product and rotating menus, it’s important to meet with your above noted vendors, tour their facilities (if possible), and implement a back-up plan. Be proactive by developing a relationship with a primary supplier and secondary supplier for each of your core food and beverage products and ingredients to reduce the risk of not only running out of fresh inventory, but being quickly prepared in the case of a recall from your primary supplier. Lastly, when meeting with them, discuss their traceability program. If they don’t have one, simply move onto the next!
Data and Software
Data continues to define restaurants and food service businesses, and data within the supply chain is no different. Many Point-of-Sale (POS) companies have come to understand the current need for better inventory and supply chain management software, which will better track shipments, local SKUs, and improve vendor communication.
Having transparency throughout the supply chain will not only position you and your concept to make solid business decisions, but it will also help protect you through deeper HACCP compliance and SKU tracking, from the day of ordering the product to the day your customer arrives to eat or drink the product.
Operation Manuals
Basic manuals will always create a sense of accountability — an effective manual will not only identify product specifications and supply chain information for each product, but will also provide solutions to quickly respond to a food safety crisis if one were to happen.
Safely managing food safety is an ongoing process that requires commitment, communication, correct processes, vigilance, and teamwork at a multitude of levels. Ensure your values meet the values of your supplier and that there is a programmed system of communication in the event of a crisis.
In most cases, the paying customer wants high-quality product at the lowest price possible. Rising food costs — and the known importance to keep these costs within a certain percentage of sales — can often lead to a link within the supply chain breaking through poor decision making and quality control.
It should be no surprise, however, that supply chain management is the means to enhancing food and beverage quality and safety, all while reducing and controlling your costs. At the end of the day, the right supply chain can actually be used as one of your best marketing tools and simply cannot become overlooked or cheated on.